Linde Warehouse Navigation
Travel Unerringly through the High Rack Warehouse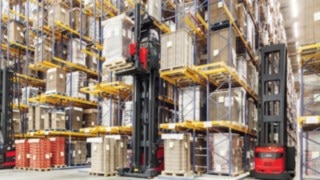
With its narrow pathways and high lifting heights, narrow aisle storage facilitates a high storage density. But this cost-effective storage method comes at a price as it places high demands on the driver and the truck. Due to the large number of storage locations available, the driver has a multitude of possible target coordinates. Keeping all these storage locations in mind and getting to them as quickly as possible is a huge challenge, which is why pallets are often stored in the wrong place.
In order to avoid errors like this and to maximize productivity in the warehouse, companies are looking for ways to identify the sources of errors in advance and show the drivers the most efficient path between the two points in the high rack at all times. Linde Warehouse Navigation helps to do this and significantly improves productivity in narrow aisle warehouses.
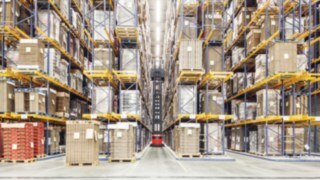
THE NAVIGATION SYSTEM FOR YOUR WAREHOUSE
Linde Warehouse Navigation communicates with the customer’s warehouse management system via Wi-Fi and assists with the acceptance and fast processing of transport orders. As soon as the driver has driven into the correct aisle, the warehouse navigation system guides them to the destination specified by the warehouse management software.
The display in the truck shows the driver both their own position in the aisle and the position of the goods that need to be moved next. The driver confirms that the order has been completed and transmits the information via Wi-Fi to the warehouse management system, which then immediately sends the next order. If the driver has used the optional fork cycle to move a full pallet, the truck automatically confirms that the order has been completed.
The truck records its position in the respective rack aisle using RFID tags or barcodes that are embedded in the floor along the rack aisles or attached to the rack. The warehouse navigation system uses these to calculate the fastest and most efficient route to the next batch of goods and optimally coordinates the truck’s driving and lifting movements.
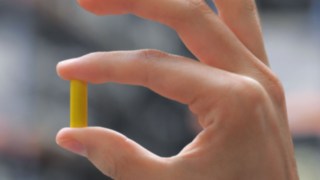
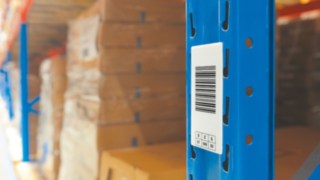
In the rack aisle, the driver merely activates the control lever. After that, the truck positions itself at the destination. For whole-pallet handling, the warehouse navigation system automatically puts the prongs into the optimal position so that the driver can then activate the optional fork cycle for storage and retrieval in order to move the next pallet. The cab’s ergonomic design allows the driver to reach goods easily when picking orders. This semi-automated process takes the strain off the driver and reduces driver error thereby increasing handling performance.
The driver can make manual corrections in both a vertical and horizontal direction, without the programmed transport order expiring. This enables pallets to be repositioned if they were not stored correctly, for example. The original transport order is then continued.
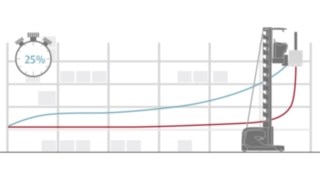
Reach your Destination Faster
Linde Warehouse Navigation enables time savings of up to 25 percent and shows the driver the fastest possible route to their destination (blue).
System Benefits at a Glance
- Storage and picking errors are excluded
- Equivalent turnover for all employees
- Storage locations accurately reached
- Potential productivity increases of up to 25 percent
- Optional automatic fork cycles make working easier
- New employees can get up to speed quickly
Ready for Operation at All Times
Linde Warehouse Navigation can be adapted to any warehouse. This is made possible by an interface on the truck, which can be used to connect a data terminal or the company’s warehouse management system. The whole system can be programmed for different hall heights, aisles of different lengths and various rack heights. In the event of changes to the warehouse structure, these parameters can also be adjusted retrospectively.
Linde Warehouse Navigation can be used on its own or in combination with Linde’s aisle safety assistant. The aisle safety assistant helps to prevent damage to the warehouse facilities as the truck and the software are precisely tailored to the warehouse.
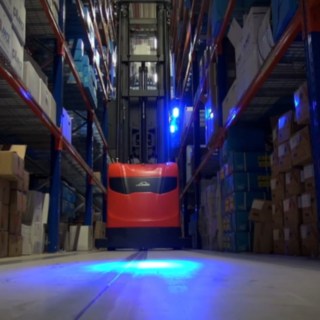